Factors Affecting Wrap Rates in Government Contracting
Unveiling the Key Influencers
Wrap rates play a significant role in government contracting, determining the reimbursement of indirect costs incurred by contractors. Understanding the factors that affect wrap rates is essential for contractors to accurately estimate costs, remain competitive, and ensure compliance. In this blog post, we will explore the key factors that influence wrap rates in government contracting, shedding light on how these factors impact financial performance and decision-making.
Indirect Cost Structure:
The structure of indirect costs is a crucial determinant of wrap rates. Contractors with higher indirect costs, such as those in complex industries or with extensive administrative needs, will generally have higher wrap rates. Conversely, companies with lower indirect costs may have lower wrap rates. Understanding your specific indirect cost structure and how it aligns with industry standards is vital for setting appropriate wrap rates.
Contract Type:
The type of contract being pursued or performed can significantly impact wrap rates. Different contract types, such as firm-fixed-price (FFP), cost-plus-fixed-fee (CPFF), or time and materials (T&M), have varying levels of risk and required resources. Contracts with higher risk or greater complexity often necessitate higher wrap rates to account for the associated indirect costs. Contractors should carefully analyze the contract type and its requirements to determine the appropriate wrap rate for each engagement.
Government Regulations:
Government regulations, such as the Federal Acquisition Regulation (FAR) and the Defense Contract Audit Agency (DCAA) guidelines, play a crucial role in setting and governing wrap rates. These regulations provide standards for allowable costs, cost accounting practices, and the calculation of indirect rates. Contractors must ensure compliance with these regulations when establishing their wrap rates to avoid financial penalties or contract disputes.
Company Size and Overhead:
The size of the contracting company and its overhead structure can impact wrap rates. Larger companies may benefit from economies of scale, allowing them to distribute indirect costs across a broader base and potentially lower their wrap rates. On the other hand, smaller companies with limited resources and higher overhead may have higher wrap rates. Contractors should consider their company size and overhead structure when calculating wrap rates to accurately reflect their cost structure.
Historical Data and Experience:
Analyzing historical data and past performance is essential for determining wrap rates. Contractors can leverage their previous contract performance to assess their indirect cost trends and identify areas for improvement. Understanding how indirect costs have fluctuated in the past can help contractors anticipate future expenses and set more accurate wrap rates. Additionally, contractors with a solid track record and demonstrated efficiency in managing indirect costs may negotiate lower wrap rates based on their experience.
Subcontracting and Vendor Relationships:
Subcontracting and vendor relationships can impact wrap rates, particularly when subcontracted services are a significant component of a contract. Contractors must consider the indirect costs associated with subcontracting and ensure that these costs are properly accounted for in their wrap rate calculations. Efficient management of subcontractors and strategic vendor relationships can help optimize indirect costs and potentially reduce wrap rates.
Market Competitiveness:
The competitive landscape within the government contracting market can influence wrap rates. Contractors need to consider the pricing strategies of their competitors and balance their wrap rates accordingly. Setting wrap rates too high may make it difficult to win contracts, while setting them too low may result in inadequate cost coverage. Contractors should conduct market research, evaluate industry benchmarks, and consider their unique value proposition to strike the right balance between competitiveness and profitability.
Wrap rates in government contracting are influenced by various factors, including the structure of indirect costs, contract types, government regulations, company size and overhead, historical data and experience, subcontracting relationships, and market competitiveness. Contractors must carefully consider these factors when calculating wrap rates to ensure accurate cost recovery, compliance, and financial viability.
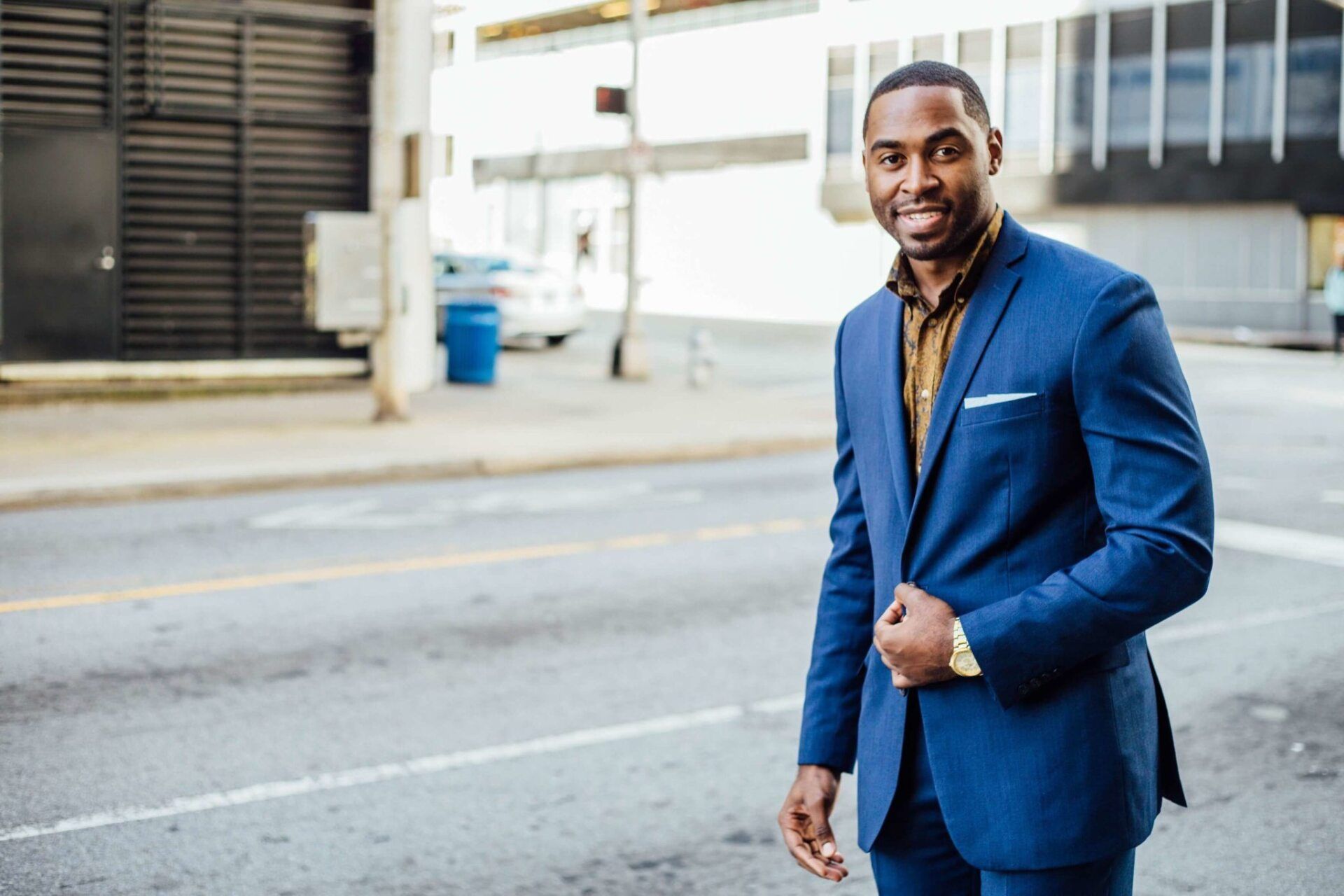
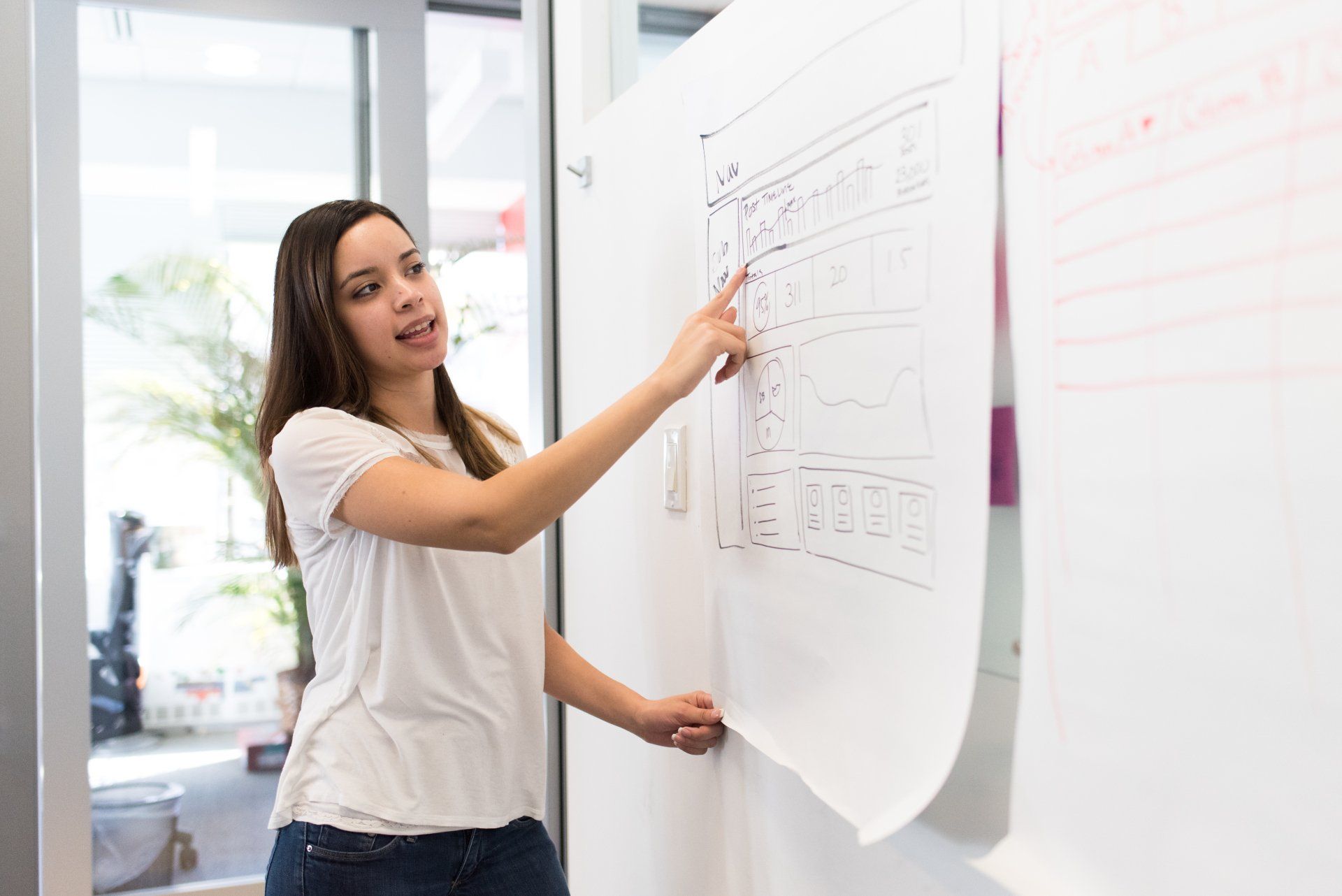
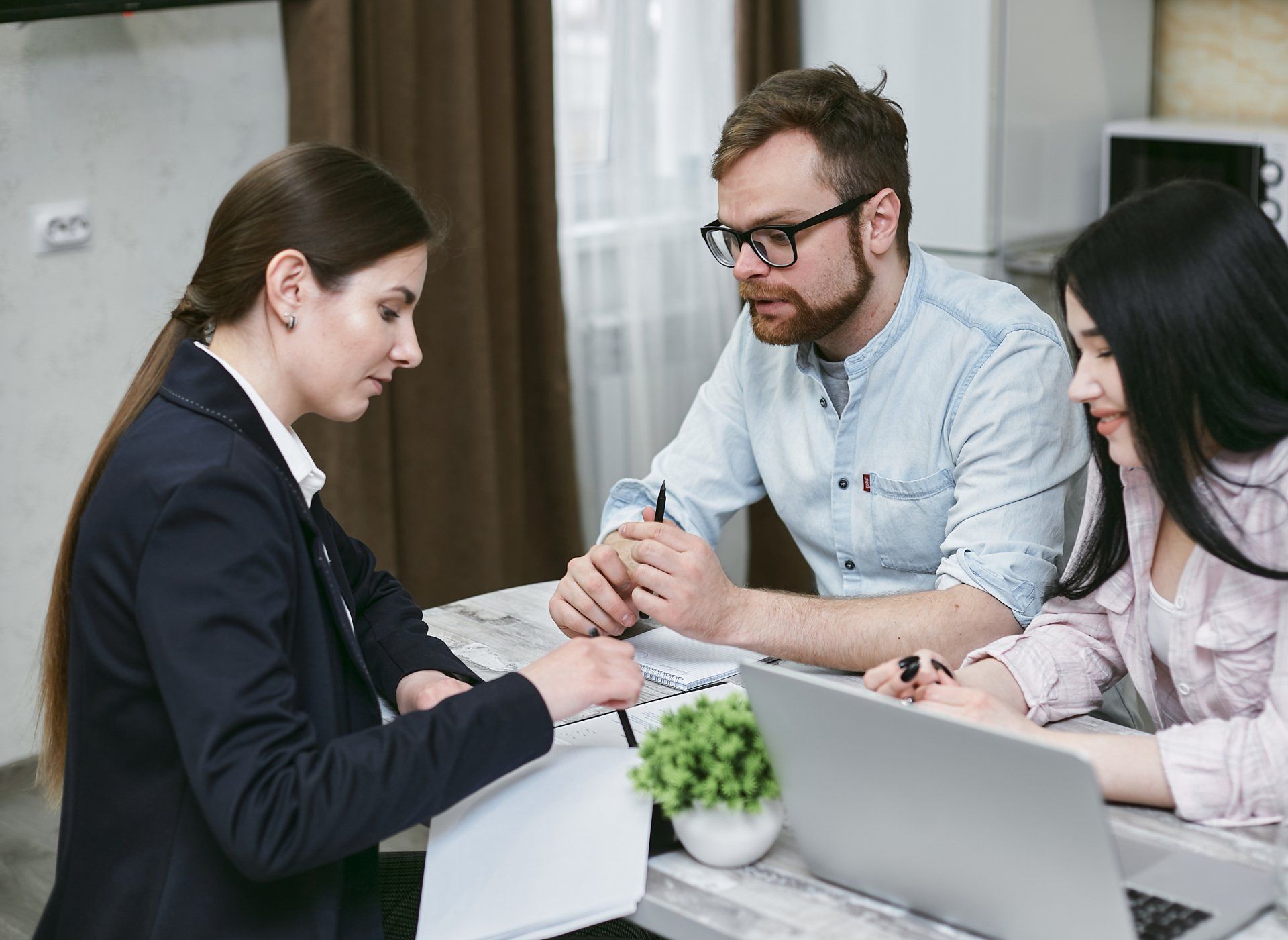
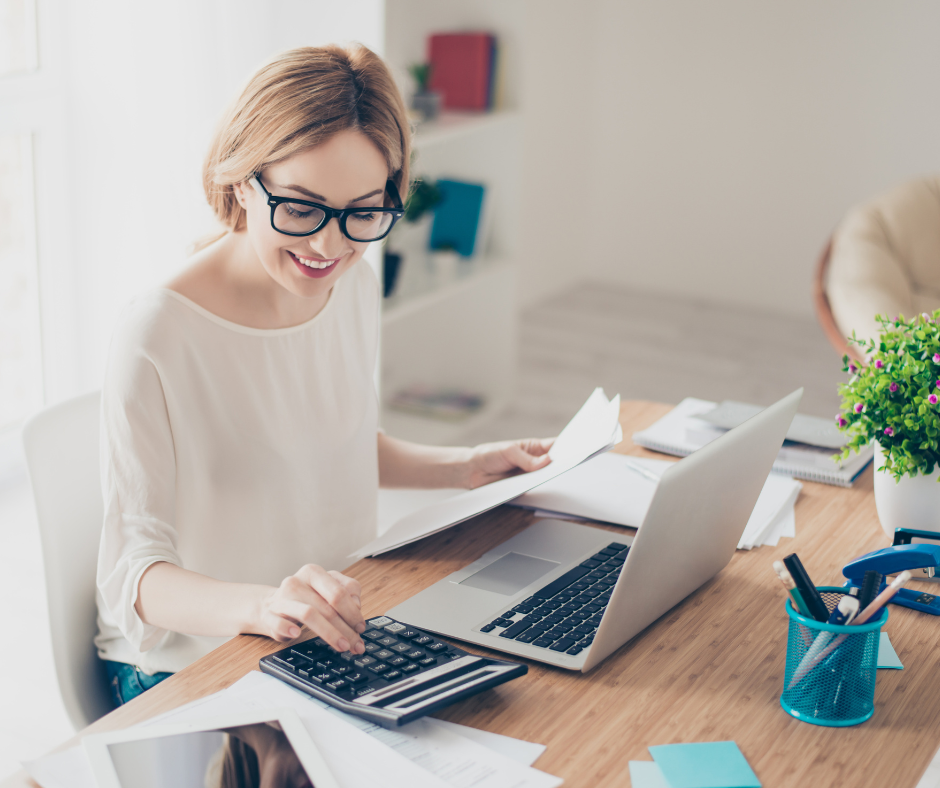
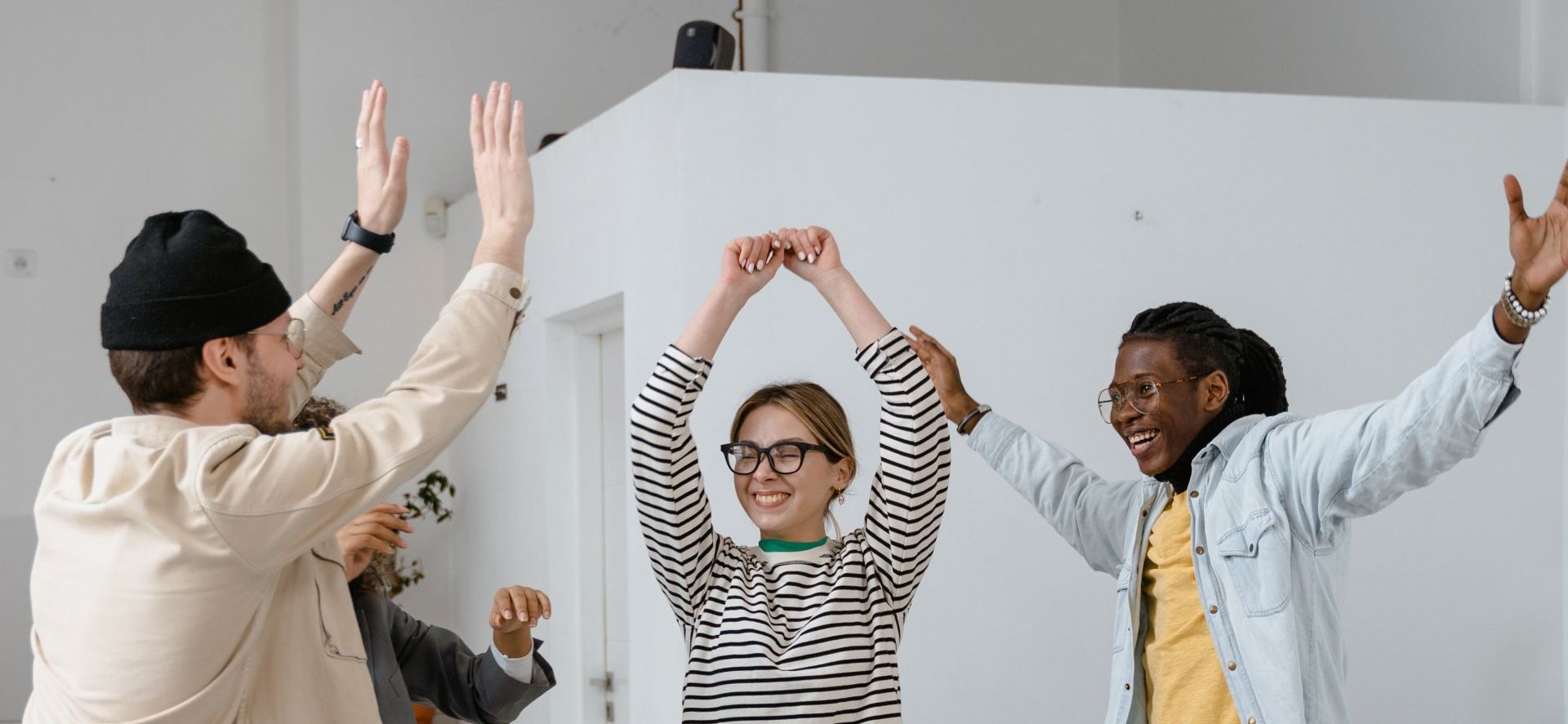
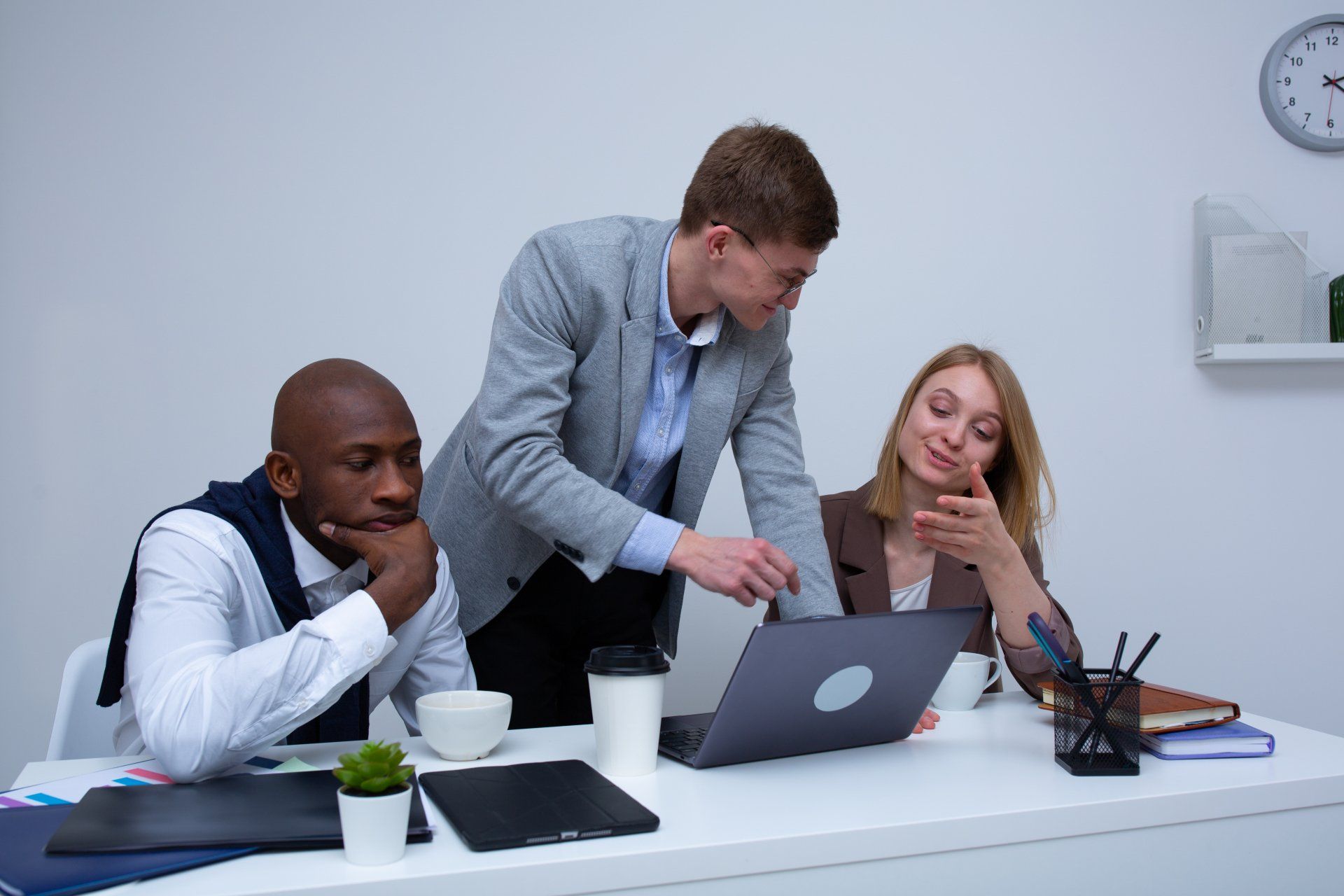
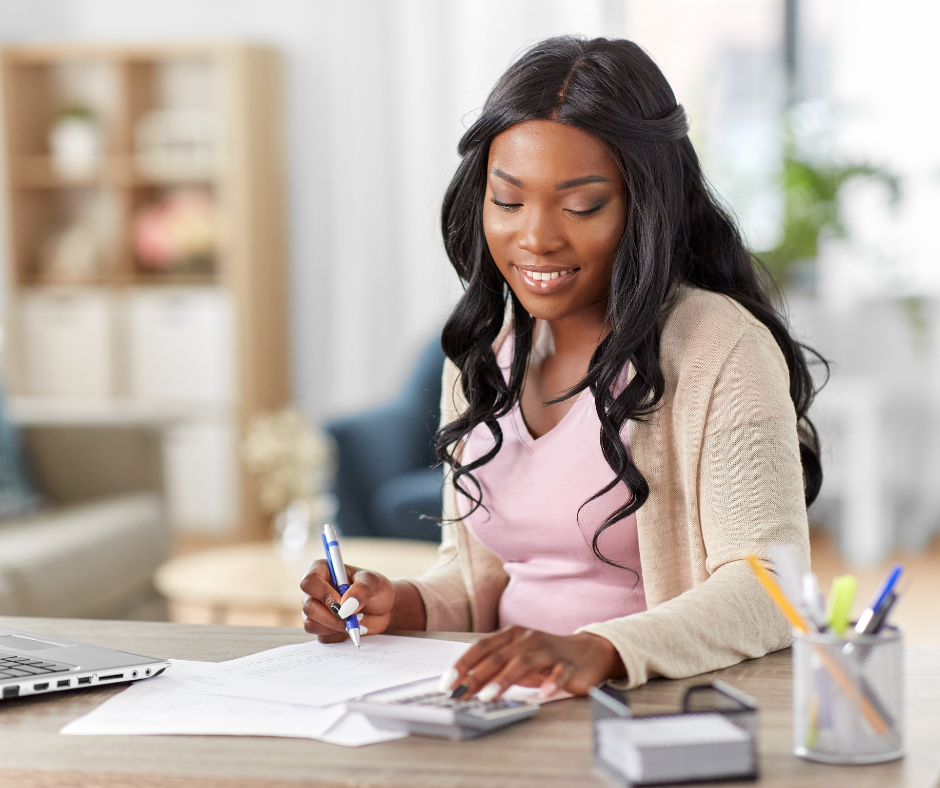
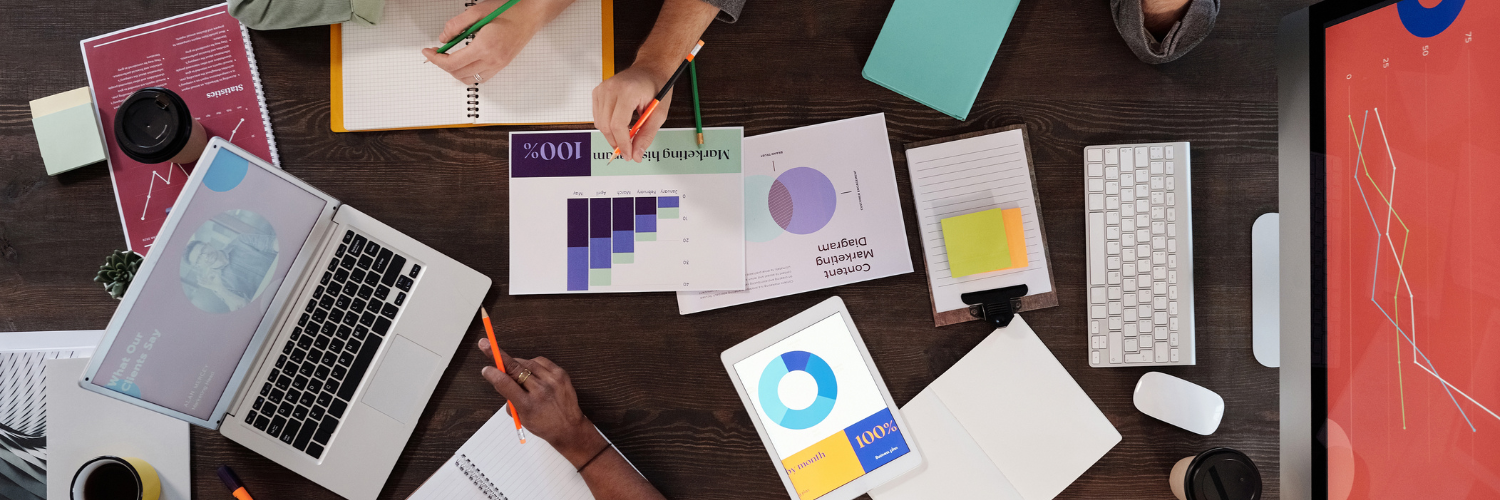